Buidling a tender for a Feldbahn
When
I decided to purchase my Feldbahn the first choice I had to make was to
specify its colour scheme, and that was simple. It had to be the
same yellow as my previous Stafford as so many people recognised that
as being my engines colour that it had almost become a corporate image.
The second choice was the design of the driving truck and that
was more difficult because I had spotted the engine shown here.
This preserved Orenstein & Koppel 0-6-0 is currently running
on the Statfold Barn Railway but originally operated in the SRAGI sugar
plantation in Java. Ideally I would have liked my Feldbahn to
look like this but Station Road Steam did not sell it with this style
of cab. However I did mock up a tender from cardboard to fit my
existing driving truck chassis but it looked awful being far too long.
So that's where things should have ended but the dream of
converting my Feldbahn wouldn't go away.
In the summer of
2015 I started to seriously look at designing a new tender for my
Feldbahn based on the one in the photo. I had found a lot more
photographs of SRAGI No 14 and to make it look right the tender had to
be short, but I wanted a similar wheelbase to my existing driving truck
to ensure stability. My eventual design retained the previous
driving truck wheelbase but unlike the real tender I positioned the
axles as close as possible to the ends of the tender. Another
full size cardboard mock-up proved that the design looked correct and
that the seating position would be both practical and comfortable.
The tender design also looked "right" when placed behind the
stock Feldbahn engine.
|
My
completed design had two major components, the chassis and the tender
body. The chassis was to be laser cut from 6mm mild steel plate
and would be within my welding capabilities once jigged up. The
body was simply too difficult for me to construct myself as it required
several different bend radii and had to have a watertight non rusting
tank incorporated into it. After talking it through with a couple
of local sheet metal fabricators I decided that it would be built from
3mm thick aluminium sheet and seam welded. Once I had completed
all the CAD drawings I accepted the quoted price and construction was
underway.
Exactly to schedule the body was ready for
delivery on December 23rd, so I received an early Christmas present !
This photo shows the body as delivered from the fabricators.
At the rear (left of the photo) is an L shaped water tank that
holds 8 gallons of water. At the front is the coal space which
can hold about 30 lbs of coal, and in the centre is space for all the
tools and other items needed for a day at the track. The narrower
section at the front allows the drivers feet be positioned nice and low
outside the tender. Personally I find this to be a comfortable
driving position and it overcomes the problem I have seen on so many
other tender designs of having the drivers feet positioned together
inside the tender and ahead of the front axle. The tender is much
more stable in this configuration as the driver's feet effectively put
their weight on the centre line of the front axle so that the tender
does not tip up as the driver climbs aboard. As will be seen
later, some careful design touches have made these wells look like part
of the design and not at all awkward. The small flat inset above
the right hand foot well is reserved for the speedometer and water
level gauge. |
While
the fabricators were building the tender body I had been progressing
with the chassis and this photo shows it jigged up ready for MIG
welding. The two solid round steel bars are simply jig beams to
correctly space and align the chassis sides. These would be removed after the
welding was complete. As these were too large to face, drill, and
tap on my lathe I asked a local machine shop to make them and they very
kindly only charged for those operations and not for the material,
provided that I returned the parts to them after use. A few more
pennies were thus saved !
Various brackets were also welded
in to support parts of the vacuum braking system, footrests, and
to mount the tender body. I don't think that I have ever placed
so much faith in my CAD design being accurate before. With most
of those brackets having been drilled before welding the design had to
be right first time, and thankfully everything worked out OK.
|
This
photo shows the chassis during installation of the vacuum braking
system. The vacuum servo is just in front of the rear axle (left
hand side of the photo) and the red painted longitudinal bracket to the
rear of the servo will eventually be used to secure the various pipes
and cables using tie wraps. The vacuum brake reservoir is on the
right hand side of the chassis between the axles, while the copper tube
will become the pipe that takes water from the tender tank to feed it
to individual connections for the two locomotive injectors.
The
PNP Railways wheels and axles are mounted using "take up bearings"
which provide a very convenient solution to axle boxes and suspension.
All you have to do is get the right springs fitted to carry the
load, and that is something I never seem to get right first time
despite hours of calculation using spreadsheets. The only
disadvantage to take up bearings is that they only seem to come painted
green, so I had to get them grit blasted before treating them with Metal
Black to obtain black coloured axle boxes. |
This
photo shows a close up of one of the take up bearings. You can
see how a 3mm thick U shaped keeper retained by four 2 ba bolts is used
to thicken the 6mm thick chassis so that the take up bearing slides
smoothly. The suspension spring simply drops into the top of the
bearing and locates around a lug formed when the chassis side was laser
cut.
The brake linkage compensator can also be seen in this
photo. The brake bar cross beams link back to the servo operating
lever which pivots in slotted brackets attached to the chassis.
This allows the operating lever to adjust its position and thus
apply equal pressure to the brakes on both axles. If the lever
simply pivoted around a fixed pivot it would be very difficult to set
the brake linkages up to ensure even brake block pressure on both axles. |
This
photo shows the completed tender coupled to my Feldbahn. You can
see how the foot rests are positioned in relation to the front axle to
ensure stability and how the inset section of the tender body allows
the drivers feet and legs to fit low and as close to the wheels as
possible. By adding handrails and chequer plate to match the
dummy steps fitted to the Feldbahn the foot rests don't look too out of
place. The
padded driver's seat acts as a cover to the central
storage section of the tender and the water tank has been deliberately
raised behind the seat to deter drivers from sitting too far back and
upsetting the stability of the tender. Laser cut side rails
finish the tender sides in a similar fashion to that of the full size
tender. Note how the sides of the tender and the bulkhead behind
the driver's seat are raised above the top of the water tank so
that any over spill when filling will drain off the back of the tender
and not spill onto the driver's seat. The water tank has a hinged
lid (which prevents it from getting lost) but as I discovered it makes
a surprisingly good seal against the tank rim. Thankfully I found
this out when testing the tender for water tightness before use because
the water flow from the injector feed pipes was quite low. Adding
a goose neck breather to the top of the tank overcame that problem.
Having
used the tender with the Feldbahn I am pleased to say that it has met
all my objectives, is very comfortable, and rides rough track very
well. The firing irons fit comfortably on top of the coal and
although the driver sits quite close to the Feldbahn there is no
problem when firing while driving. With so much coal and water
onboard you can happily stay out on track and away from water or
coaling facilities for several hours at a time if just pottering about.
Since
completing the tender two changes have been made to it. The
first, the goose neck breather, has already been mentioned. This
was fabricated by silver soldering a pair of 8mm copper elbows together
because normal tube benders simply can't bend pipe tight enough.
There is a photo of the finished goose neck below. The second
change was the addition of a water filter into the injector feed pipe.
Neither my Stafford or Feldbahn have ever had water filters
fitted in their injector feeds, but between them they have covered over
700 miles with only one incident when a piece of debris stopped an injector
from working. However a water filter has always seemed like a
good idea that I have never got around to until now. A chance
observation when searching on-line for spares for my lawn mower
resulted in me spotting an in-line water filter suitable for 16mm
(5/8") pipe, which by a happy coincidence is the diameter of the water
feed pipe under the tender. Having bought one of the filters I
found that it can easily be dismantled for cleaning and that the mesh
filter inside it looks perfect for filtering injector feed water.
The photo below shows it installed underneath the tender.
The
other photo below shows the speedometer mounted at the front of the
tender. Behind it is a small box with a switch to control the
brightness of the Feldbahn's headlamp; H (bright), L (dim) with a
centre Off position. If either headlamp brightness is selected
the train tail lamp is also switched On. The box also has three
LED's fitted (Green, Yellow, and Red when lit) which show the driver
how much water is left in the tender. Two magnetic float switches
(more normally used in fish tanks) are fitted in the water tank which operate relays to illuminate one LED
at a time. The position of the float switches was set so that the
Green LED is lit for anything over 1/2 a tank of water, the Yellow LED
for 1/4 to 1/2 a tank, and the Red LED for less than 1/4 of a tank.
Power for the level indicators and lights comes from a 12V NiCad
pack stored in the tender's tool space.
|
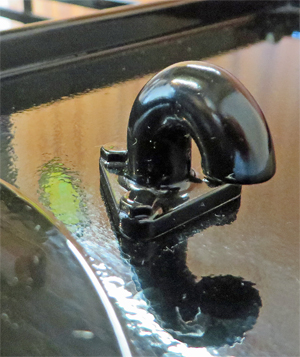 | 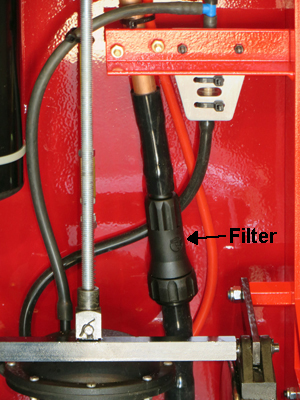 | 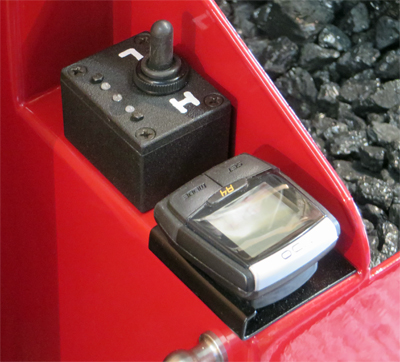 | The water tank goose neck vent. | The in-line water filter. | Tender displays and light switch. |
|